Additive manufacturing is an alternative to traditional machining processes such as CNC and injection molding. It uses a layer-by-layer process to build up a part from raw materials.
Prototypes can be printed and iterated quickly without the need for costly moulds. This reduces design risk and enables products to reach the market far faster. Click https://www.by3design.com/ to learn more.
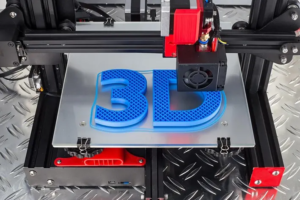
- Direct Energy Deposition (DED)
Direct energy deposition (DED) is a metal 3D printing technology that works with metals and alloys, particularly titanium, Inconel, and steel. It can be used to create parts with complex geometries and internal features. The process uses a wire or filament as the feedstock material that is melted by a heat source to build up the part layer by layer.
The heat source can be an electric arc, a laser, an electron beam or a plasma arc. Laser-based DED is the most commonly used type of metal 3D printing, including methods like laser engineered net shape, laser light fabrication, directed light fabrication and electron beam additive manufacturing (EBAM).
DED systems are capable of working with a wide range of feed materials. These can be introduced through a powder blend or multiple filament feeds, and the composition of these materials can even be varied during fabrication.
A key factor for success with DED is the ability to maintain a high level of accuracy and control the grain structure of the deposited material. This helps reduce porosity, which can be an issue with this type of 3D printing. Another critical element is the power of the heat source, which can impact both the size of the melt pool and the cooling rate.
DED is a good choice for manufacturing components with tight tolerances and complex geometries. However, its initial costs can be expensive. Furthermore, it requires a skilled workforce to operate the equipment and maintain optimal print quality. It also can be less efficient than other powder bed fusion (PBF) machines when building mid-size metal parts. For example, research has shown that DED is ten times faster and five times cheaper than PBF when building a 150mm diameter and 200mm tall Inconel metal part.
- Material Jetting
Using a powder base and liquid binder, material jetting operates by printing layer-by-layer. This technique can build up intricate structures and creates high-resolution items, particularly for objects that require complex geometries.
It is also ideal for printing full-colour, visual prototypes, injection moulds and casting patterns. Developed in the 1990s, it has become one of the most popular 3D printing technologies.
Unlike the sintering and melting methods of FDM and SLS, which use laser beams, electric arcs and electron beams to melt materials together, material jetting uses a photopolymerisation process that cures the material with UV light in a similar way to photographic film development. Material jetting can also use multiple different colours and materials within the same print, which offers designers a wider range of possible design options and allows them to create realistic prototypes with smooth surfaces.
The printer’s print head has multiple nozzles, which can be set to deposit various different materials and/or colours simultaneously. This can be used to make coloured or translucent parts, and the nozzles can even be positioned to print multiple colours onto the same object. The printer can also build support structures for the printed part, which are made from a dissolvable material that can be easily removed during post-processing without leaving any marks on the finished print.
The ability to turn CAD models into physical parts, with the option of creating multiple iterations, speeds up product development and helps companies avoid expensive mistakes that could be costly in production. Furthermore, the ability to produce a finished item in hours means that companies can keep manufacturing in-house and protect intellectual property. 3D printing can also provide cost savings and reduced time to market when compared with traditional methods of producing parts, and can be more environmentally friendly.
- Selective Laser Sintering (SLS)
Selective laser sintering (SLS) is a method of 3D printing that uses a high-powered laser to “sinter” small particles of polymer powder into a product based on a CAD model. It’s one of the most reliable, precise and fast methods for prototyping and small batch production of end-use parts. SLS is especially suited for plastic materials with good mechanical properties such as Nylon PA 12.
The SLS process works by depositing layers of a chosen polymer powder into a build chamber. During the fabrication, a CO2 laser beam is used to scan over the surface of the layer. This is followed by a heat-source to melt and fuse the melted powder into place. This is repeated until the final part has been built. Unlike FDM, SLS printing does not use support structures which gives designers a lot more scope for their designs.
However, the quality of SLS printed parts is impacted by a variety of factors. A major problem is porosity that results from entrapped air between the matrix and reinforcement materials. This can be caused by the shape and reusability of the powder, as well as by the laser power or scanning speed. Hatch spacing, which controls the level of overlap between laser scans, also has a significant impact on part density and strength.
To overcome these challenges, proper monitoring and control is essential. This can be done using a variety of sensors and techniques such as fringe projection, laser profilometers and thermal infrared cameras. Unsupervised machine learning models can also be trained on process data to detect anomalies and alert operators when they occur. For example, convolutional neural networks have been shown to be effective at identifying defects in SLS.
- Fused Deposition Modeling (FDM)
Fused deposition modeling (FDM) is a popular method of 3D printing and is used in many desktop printers. It works by heating a thermoplastic material and depositing it onto a platform layer by layer until the final model is formed. It is a great option for prototyping, allowing engineers to test their design in physical form and get feedback before committing to larger scale production.
Before a part can be printed, it must be converted to a file format that the printer understands, typically an STL file. Then the software will “slice” the model into layers that can be built upon one at a time. The sliced model is then sent to the printer where molten thermoplastic is deposited onto the platform in the dictated shape.
The melted thermoplastic is then allowed to cool before more layers are added. The process is repeated until the final product is complete. As this type of printing uses a thermoplastic, it is best for producing parts that need strength, durability and chemical resistance. In addition to plastics, other materials such as metals and ceramics can be printed using this technique.
Regardless of the printing process, it is important that the final printed item is accurate and has a good surface finish. Many desktop printers have lower tolerances than industrial machines and parts produced by this method may have visible layer lines that need to be smoothed out during post-processing.
The quality of the finished part can be improved by changing the material being used and increasing the print speed. In addition, the ability to reduce energy consumption and to use renewable natural polymers can help to make the process more sustainable.
- Material Extrusion
Material Extrusion is the method of 3D printing that most people are familiar with, as it is used in many home- and hobby-grade printers. It works by forcing a spool of thermoplastic polymer through a heated nozzle, which deposits the material layer-by-layer onto a build platform. This technology is known by a variety of names, including fused filament fabrication (FFF) and fused deposition modeling (FDM).
The material that is printed with this technology can be both flexible and rigid. It is also capable of printing with a range of materials, from plastics to rubbers and even metals, making it well suited for creating functional engineering prototypes and systems. In addition, it has the capability to print a wide range of colors, which can give a product a more vibrant and attractive appearance.
While this technique is relatively inexpensive and easy to use, it does not have as high of a resolution as other 3D printing methods. It also has a tendency to create prints with noticeable layer lines, which can require additional post processing work to achieve a smooth surface finish.
It is important to understand the different capabilities of each printing method before choosing one that will best suit your needs. Whether you are just starting out or are a seasoned professional, 3D printing can help you reduce your manufacturing time and costs, while improving your quality, efficiency, and productivity.
If you need support with your 3D printing projects, contact TWI’s Industrial Members for world-class expertise in a wide range of additive technologies and materials. Our experts are available to act as an extension of your own internal resources, assisting with design, development, and testing across a range of industries.